Introduction:
Battery grading (also known as battery screening or battery sorting) refers to the process of classifying, sorting and quality screening batteries through a series of tests and analysis methods during battery manufacturing and use. Its core purpose is to ensure that the battery can provide stable performance in the application, especially during the assembly and use of the battery pack, so as to avoid battery pack failure or reduced efficiency caused by inconsistent performance.
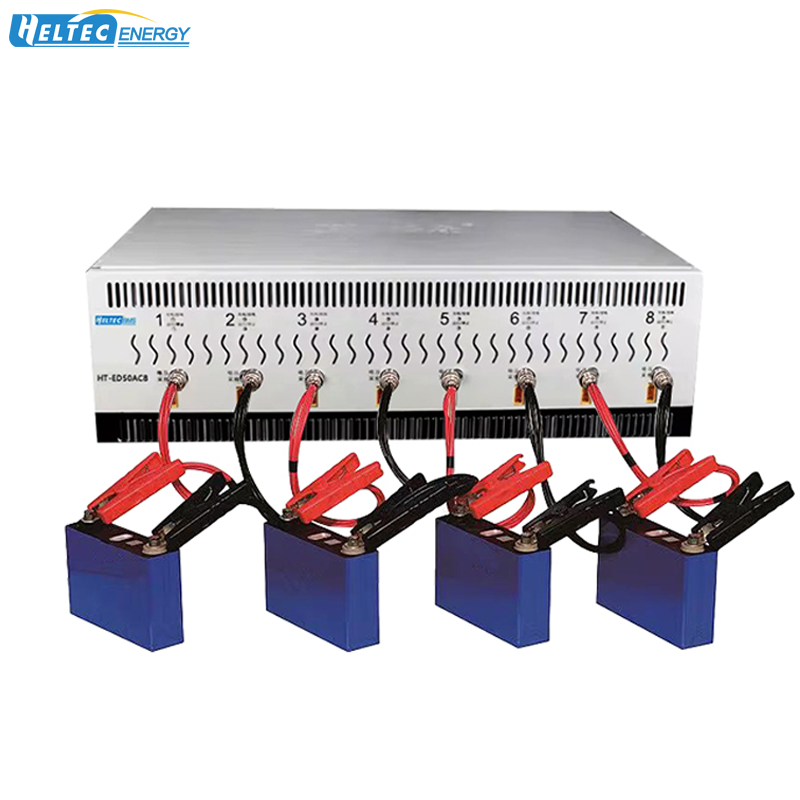
The significance of battery grading
Improve battery performance consistency: During the production process, even batteries from the same batch may have inconsistent performance (such as capacity, internal resistance, etc.) due to differences in raw materials, manufacturing processes, environmental factors, etc. Through grading, batteries with similar performance can be grouped and used to avoid cells with too large performance differences in the battery pack, thereby improving the balance and working efficiency of the entire battery pack.
Extend battery life: Battery grading can effectively avoid mixing poor-performance batteries with high-performance batteries, thereby reducing the impact of low-performance batteries on the overall life of the battery pack. Especially in battery packs, performance differences of certain batteries may cause premature decay of the entire battery pack, and grading helps to extend the service life of the battery pack.
Ensure battery pack safety: Differences in internal resistance and capacity between different batteries may cause safety problems such as overcharging, over-discharging or thermal runaway during battery use. Through grading, battery cells with consistent performance can be selected to reduce the mutual influence between mismatched batteries, thereby improving the safety of the battery pack.
Optimize battery pack performance: In the design and application of battery packs, in order to meet specific energy requirements (such as electric vehicles, power storage systems, etc.), a group of battery cells with similar performance is required. Battery grading can ensure that these battery cells are close in capacity, internal resistance, etc., so that the battery pack has better charging and discharging performance and efficiency as a whole.
Facilitates fault diagnosis and management: The data after battery grading can help manufacturers or users better manage and maintain batteries. For example, by recording the battery grading data, the battery degradation trend can be predicted, and batteries with greater performance degradation can be found and replaced in time to avoid affecting the entire battery system.
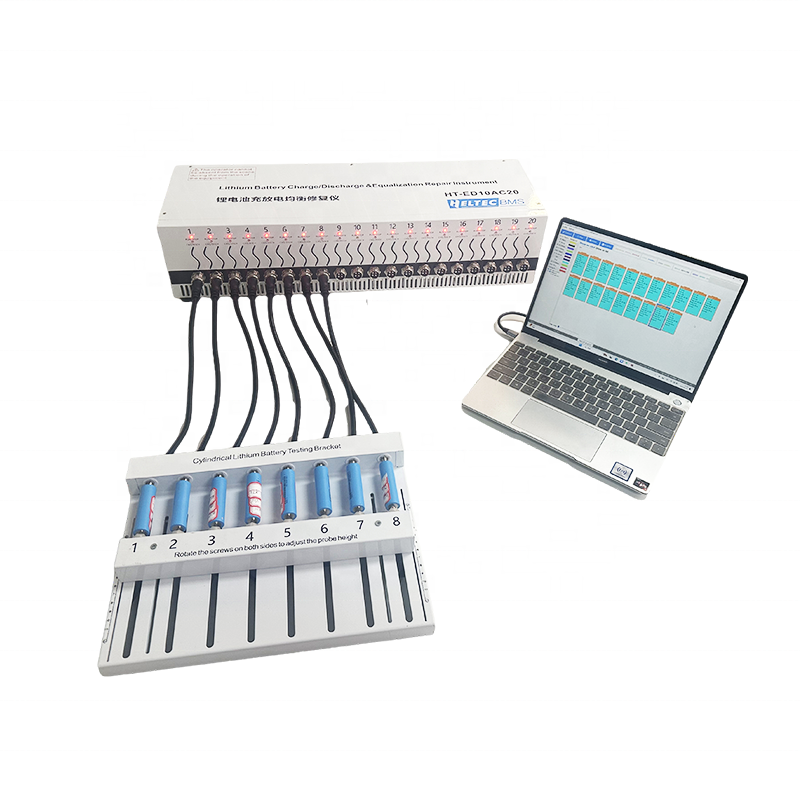
Principles of battery grading
The process of battery grading usually relies on a series of performance tests on the battery, mainly based on the following key parameters:
Capacity Tester: The capacity of a battery is an important indicator of its energy storage capacity. During grading, the actual capacity of the battery is measured through a discharge test (usually a constant current discharge). Batteries with larger capacities are usually grouped together, while batteries with smaller capacities may be eliminated or used in combination with other cells with similar capacities.
Internal resistance tester: The internal resistance of a battery refers to the resistance to the flow of current inside the battery. Batteries with larger internal resistance tend to generate more heat, affecting the efficiency and life of the battery. By measuring the internal resistance of the battery, batteries with lower internal resistance can be screened out so that they can perform better in the battery pack.
Self-discharge rate: The self-discharge rate refers to the rate at which the battery loses power naturally when it is not in use. A higher self-discharge rate usually indicates that the battery has certain quality problems, which may affect the storage and use stability of the battery. Therefore, batteries with lower self-discharge rates need to be screened out during grading.
Cycle life: The cycle life of a battery refers to the number of times a battery can maintain its performance during the charge and discharge process. By simulating the charge and discharge process, the cycle life of the battery can be tested and good batteries can be distinguished from poor ones.
Temperature characteristics: The working performance of the battery at different temperatures will also affect its grading. The temperature characteristics of the battery include its performance in low or high temperature environments, such as capacity retention, changes in internal resistance, etc. In practical applications, batteries often experience different temperature environments, so temperature characteristics are also an important grading indicator.
Dormant period detection: In some grading processes, the battery will be required to stand for a period of time after being fully charged (usually 15 days or more), which can help observe the self-discharge, internal resistance change and other problems that may occur in the battery after long-term standing. Through the detection of the dormant period, some potential quality problems can be found, such as the long-term stability of the battery.
Conclusion
In the process of battery manufacturing and battery assembly, accurate battery performance testing and grading are essential. In order to ensure the quality and safety of the battery pack, it is essential to accurately screen each battery. Heltec's various battery charge and discharge test instruments are high-precision equipment tailored to this demand, which can effectively improve the battery detection accuracy and work efficiency.
Our battery capacity analyzer is an ideal tool for battery grading, screening and performance evaluation. It combines high-precision testing, intelligent analysis and efficient workflow to help you achieve higher quality control and management efficiency in battery manufacturing and application. Contact us now to learn more about battery capacity analyzers, improve battery management efficiency, and ensure the stability and safety of battery packs!
Request for Quotation:
Jacqueline: jacqueline@heltec-bms.com / +86 185 8375 6538
Sucre: sucre@heltec-bms.com / +86 136 8844 2313
Nancy: nancy@heltec-bms.com / +86 184 8223 7713
Post time: Dec-19-2024