Introduction:
Lithium battery is a battery that uses lithium metal or lithium compound as electrode material. Due to the high voltage platform, light weight and long service life of lithium, lithium battery has become the main type of battery widely used in consumer electronics, energy storage systems, electric vehicles and other fields. Today, let's explore the last few steps of lithium battery manufacturing, Formation-OCV testcapacity-Separation.
Formation
Lithium battery formation is the first charging process of the battery after the lithium battery is filled with liquid.
This process can activate the active substances in the battery and activate the lithium battery. At the same time, the lithium salt reacts with the electrolyte to form a solid electrolyte interface (SEI) film on the negative electrode side of the lithium battery. This film can prevent the further occurrence of side reactions, thereby reducing the loss of active lithium in the lithium battery. The quality of SEI has a great influence on the cycle life, initial capacity loss, and rate performance of lithium batteries.
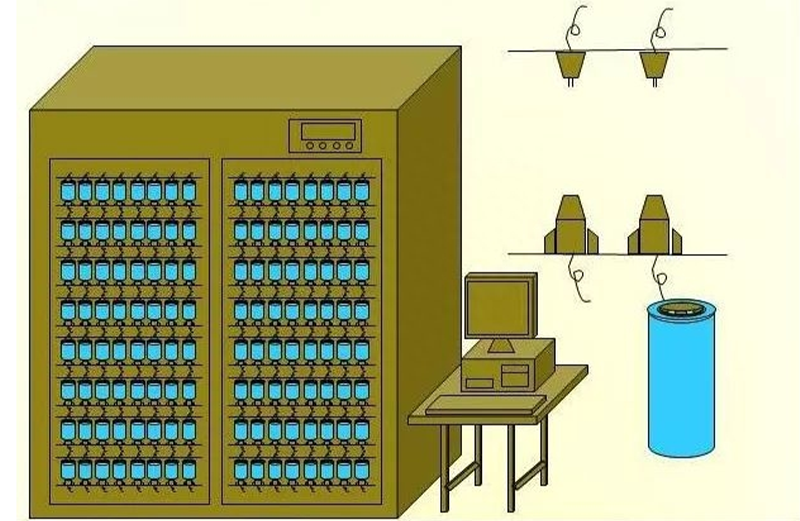
OCV test
OCV test is a test of the open circuit voltage, AC internal resistance and shell voltage of a single cell. It is a very important part of the battery production process. It needs to meet the OCV accuracy of 0.1mv and the shell voltage accuracy of 1mv. The OCV test is used to sort the cells.
OCV test production process
OCV test mainly measures the battery characteristics by pressing the probes connected to the voltage tester and the internal resistance tester on the positive and negative ears of the soft pack battery.
The current OCV test is mainly a semi-automatic test. The worker manually places the battery in the test device, and the probe of the test device is in contact with the positive and negative ears of the battery to perform OCV test on the battery, and then manually unloads and sorts the battery.
Lithium battery capacity division
After a batch of lithium batteries are made, although the size is the same, the capacity of the batteries will be different. Therefore, they must be fully charged on the equipment according to the specifications, and then discharged (completely discharged) according to the specified current. The time taken to discharge the battery fully multiplied by the discharge current is the capacity of the battery.
As long as the tested capacity meets or exceeds the designed capacity, the lithium battery is qualified, and the battery with less than the designed capacity cannot be considered a qualified battery. This process of selecting qualified batteries through capacity testing is called capacity division.
The role of lithium battery capacity division is not only conducive to the stability of the SEI film, but also can shorten the time consumed by the capacity division process, reduce energy consumption and increase production capacity.
Another purpose of capacity division is to classify and group the batteries, that is, to select the monomers with the same internal resistance and capacity for combination. When combining, only those with very similar performance can form a battery pack.
Conclusion
Finally, the lithium battery has completed all the processes of the battery cell after a full appearance inspection, grade code spraying, grade scanning inspection, and packaging, waiting to be assembled into a battery pack.
Regarding battery packs, if you have the idea of DIY battery packs, Heltec provides battery capacity testers to let you understand your battery parameters and consider whether it is suitable to assemble the battery pack you want. We also provide battery equalizer to maintain your old batteries and balance the batteries with uneven charge and discharge to improve battery efficiency and life.
Heltec Energy is your trusted partner in battery pack manufacturing. With our relentless focus on research and development, coupled with our comprehensive range of battery accessories, we offer one-stop solutions to meet the evolving needs of the industry. Our commitment to excellence, tailored solutions, and strong customer partnerships make us the go-to choice for battery pack manufacturers and suppliers worldwide.
If you have any questions or would like to learn more, please don't hesitate to reach out to us.
Request for Quotation:
Jacqueline: jacqueline@heltec-bms.com / +86 185 8375 6538
Sucre: sucre@heltec-bms.com / +86 136 8844 2313
Nancy: nancy@heltec-bms.com / +86 184 8223 7713
Post time: Nov-11-2024