Introduction:
Lithium battery is a rechargeable battery that uses lithium metal or lithium compounds as the anode material of the battery. It is widely used in portable electronic devices, electric vehicles, energy storage systems and other fields. Lithium batteries have changed our lives. Next, let's take a look at the Pole baking, Pole winding, and Core into shell in the preparation of lithium batteries.
Pole baking
The water content inside the lithium battery must be strictly controlled. Water has a great impact on the performance of the lithium battery, affecting indicators such as voltage, internal resistance, and self-discharge.
Excessive water content will lead to product scrapping, quality degradation, and even product explosion. Therefore, in multiple production processes of lithium batteries, the positive and negative poles, cells, and batteries must be vacuum baked multiple times to remove as much water as possible.
.jpg)
Pole winding
The slit pole piece is rolled into a layered core shape through the rotation of the winding needle. The normal wrapping method is diaphragm, positive electrode, diaphragm, negative electrode, and the coated diaphragm faces the positive electrode. Generally, the winding needle is prismatic, elliptical, or circular. Theoretically, the rounder the winding needle, the better the core fits, but the circular winding needle makes the pole ear fold more seriously.
During the winding process, CCD is used for detection and correction, and the distance between the positive and negative electrodes and the distance between the positive and negative electrodes and the diaphragm is detected.
Pole winding production process
The slit lithium battery positive and negative pole pieces, the negative pole pieces, and the separator are rolled together through the winding needle mechanism of the winding machine. The adjacent positive and negative pole pieces are isolated by the separator to avoid short circuit. After the winding is completed, the winding core is fixed with the tail tape to prevent it from spreading, and then it flows to the next process.
The most important thing in this process is to ensure that there is no physical contact short circuit between the positive and negative electrodes, and that the negative electrode can completely cover the positive electrode in both the horizontal and vertical directions.
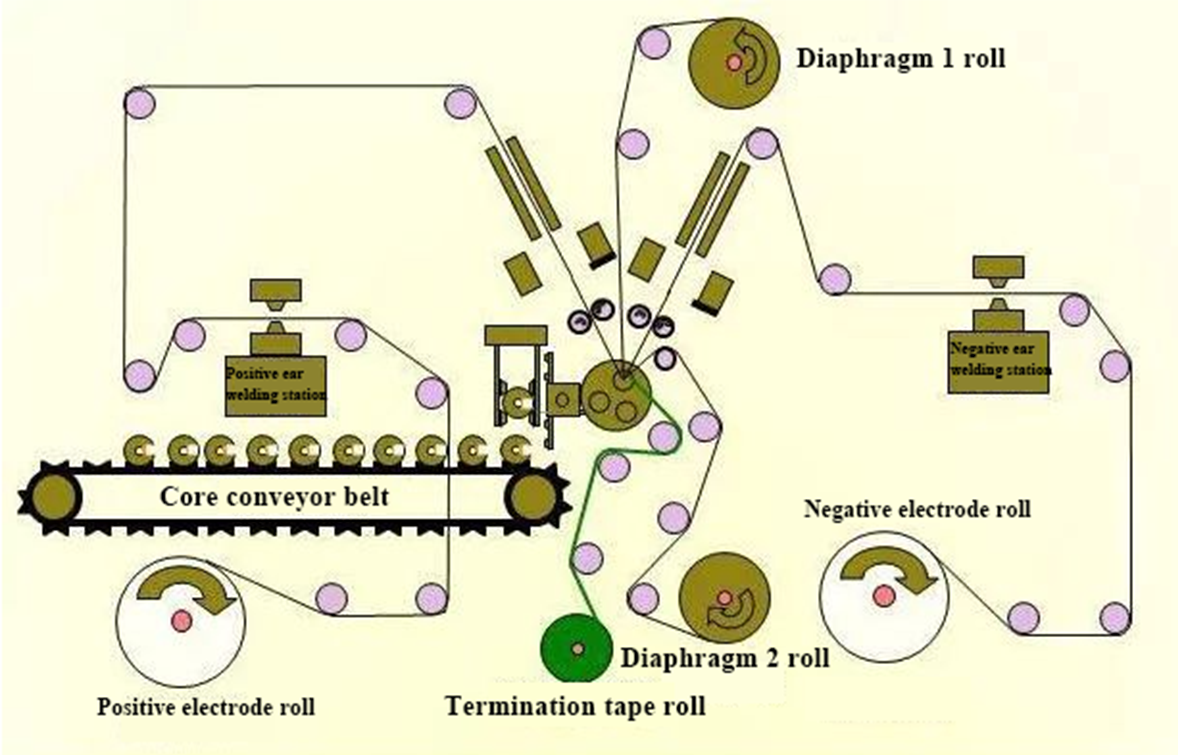
Roll core into shell
Before the roll core is put into the shell, it is necessary to perform a Hi-Pot test voltage of 200~500V (to test whether there is a high-voltage short circuit) and vacuum treatment (to further control dust before putting it into the shell). The three major control points of lithium batteries are moisture, burrs, and dust.
Roll core into shell production process
After the previous process is completed, the lower pad is placed at the bottom of the roll core and the negative pole ear is bent so that the pole ear surface faces the roll core pinhole, and finally vertically inserted into the steel shell or aluminum shell. The cross-sectional area of the roll core is less than the cross-sectional area of the steel shell, and the shell entry rate is about 97%~98.5%, because the rebound value of the pole piece and the degree of liquid injection during the later period must be considered.
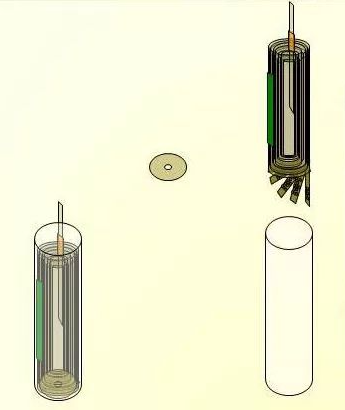
Heltec is committed to becoming a global leading lithium battery solution provider to meet the needs of all types of customers. Our company provides a variety of lithium batteries, including drone lithium batteries, golf cart lithium batteries, forklift lithium batteries, etc., to ensure that the products meet international standards and industry specifications. According to the specific needs of customers, we provide personalized lithium battery solutions, such as: capacity and size customization, different voltages and discharge characteristics. Choose Heltec and experience your lithium battery journey.
Conclusion
Every step in the lithium battery processing process needs to be strictly controlled to ensure the safety and performance of the final product. With the advancement of technology, many companies are also constantly exploring new materials and processes to improve the energy density and service life of batteries.
Heltec Energy is your trusted partner in battery pack manufacturing. With our relentless focus on research and development, coupled with our comprehensive range of battery accessories, we offer one-stop solutions to meet the evolving needs of the industry. Our commitment to excellence, tailored solutions, and strong customer partnerships make us the go-to choice for battery pack manufacturers and suppliers worldwide.
If you have any questions or would like to learn more, please don't hesitate to reach out to us.
Request for Quotation:
Jacqueline: jacqueline@heltec-bms.com / +86 185 8375 6538
Sucre: sucre@heltec-bms.com / +86 136 8844 2313
Nancy: nancy@heltec-bms.com / +86 184 8223 7713
Post time: Oct-28-2024