Introduction:
Lithium batteries are a type of battery that uses lithium metal or lithium alloy as the negative electrode material and uses a non-aqueous electrolyte solution. Due to the highly active chemical properties of lithium metal, the processing, storage, and use of lithium metal have very high environmental requirements. Next, let's take a look at the homogenization, coating, and rolling processes in the preparation of lithium batteries.
Positive and negative electrode homogenization
The electrode of lithium-ion battery is the most important component of the battery cell. The positive and negative electrode homogenization refers to the preparation process of the slurry coated on the positive and negative electrode sheets of lithium ion. The preparation of the slurry requires mixing the positive electrode material, the negative electrode material, the conductive agent and the binder. The prepared slurry needs to be uniform and stable.
Different lithium battery manufacturers have their own homogenization process formulas. The order of adding materials, the proportion of adding materials and the stirring process in the homogenization process have a great influence on the homogenization effect. After the homogenization, the slurry needs to be tested for solid content, viscosity, fineness, etc. to ensure that the slurry performance meets the requirements.
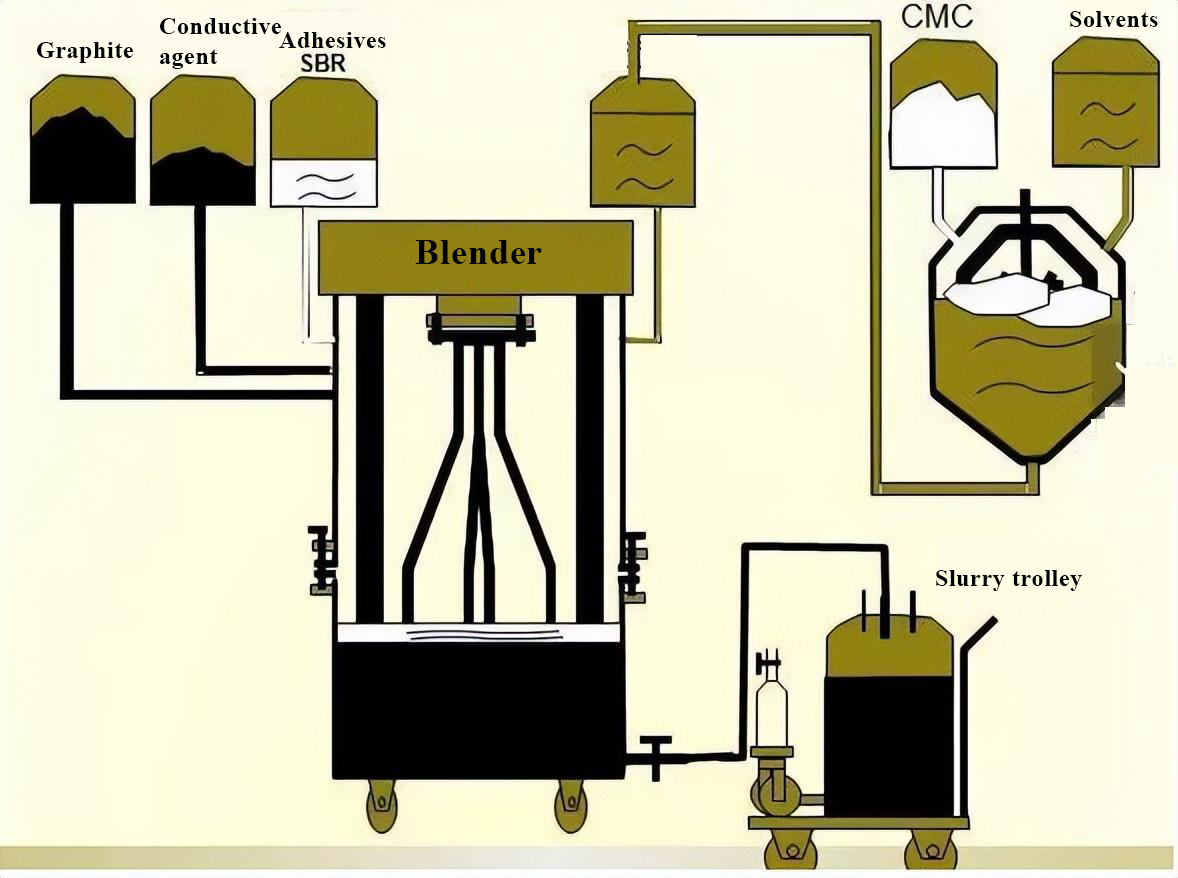
Coating
The coating process is a process based on the study of fluid properties, in which one or more layers of liquid are coated on a substrate. The substrate is usually a flexible film or backing paper, and then the coated liquid coating is dried in an oven or cured to form a film layer with special functions.
Coating is a key process in the preparation of battery cells. The quality of coating is directly related to the quality of the battery. At the same time, lithium-ion batteries are very sensitive to moisture due to the characteristics of the system. A trace amount of moisture may have a serious impact on the electrical performance of the battery; the level of coating performance is directly related to practical indicators such as cost and qualified rate.
Coating production process
The coated substrate is unwound from the unwinding device and fed into the coating machine. After the head and tail of the substrate are connected to form a continuous belt at the splicing table, they are fed into the tension adjustment device and the automatic deviation correction device by the pulling device, and enter the coating device after adjusting the sheet path tension and sheet path position. The pole piece slurry is coated in sections in the coating device according to the predetermined coating amount and blank length.
When double-sided coating, the front coating and blank length are automatically tracked for coating. The wet electrode after coating is sent to the drying channel for drying. The drying temperature is set according to the coating speed and coating thickness. The dried electrode is rolled up after tension adjustment and automatic deviation correction for the next step of processing.
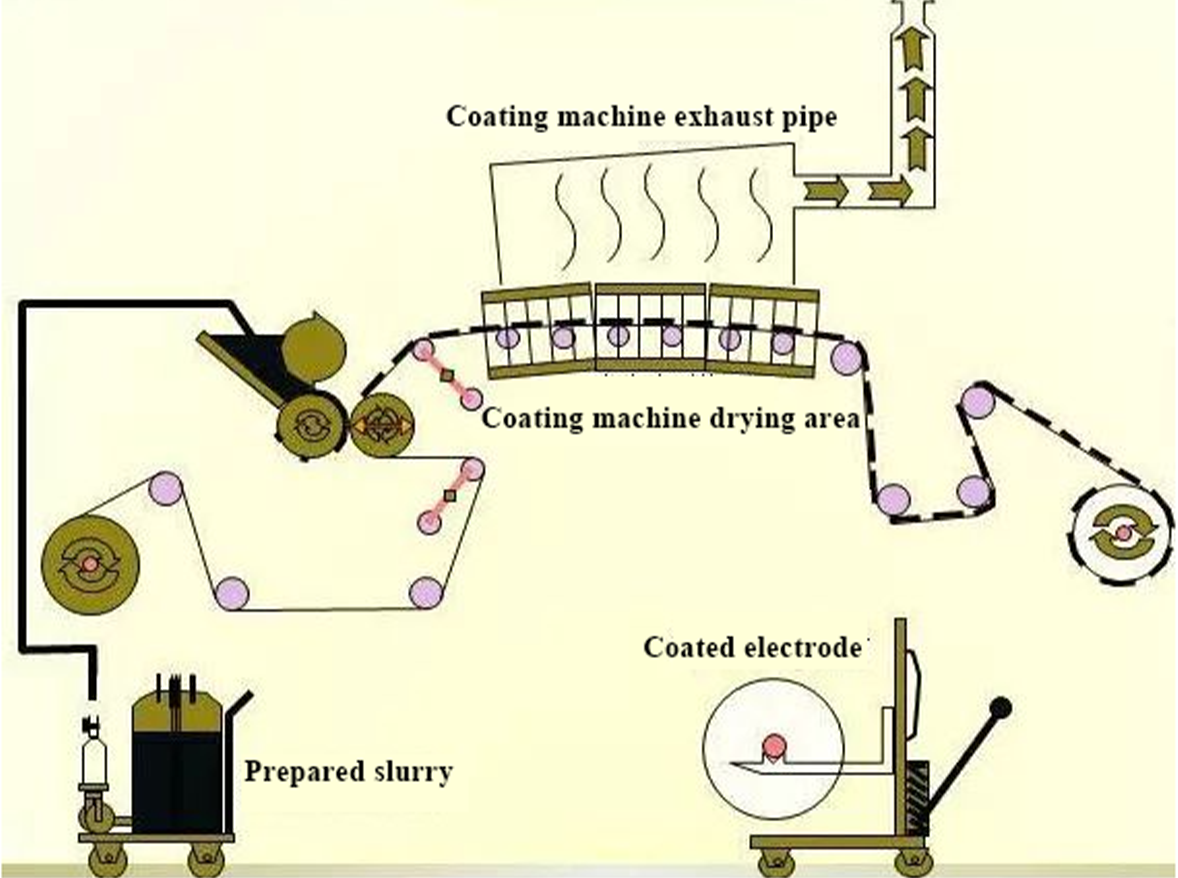
Rolling
The rolling process of lithium battery pole pieces is a production process that uniformly presses raw materials such as active materials, conductive agents and binders on metal foil. Through the rolling process, the pole piece can have a higher electrochemical active area, thereby improving the energy density and charge and discharge performance of the battery. At the same time, the rolling process can also make the pole piece have higher structural strength and good consistency, which helps to improve the cycle life and safety of the battery.
Rolling production process
The process of rolling process of lithium battery pole pieces mainly includes raw material preparation, mixing, compaction, shaping and other links.
Raw material preparation is to mix various raw materials evenly and add appropriate amount of solvent for stirring to obtain a stable slurry.
The mixing link is to mix various raw materials evenly for subsequent compaction and shaping.
The compaction link is to press the slurry through a roller press so that the active material particles are closely stacked to form a pole piece with a certain structural strength. The shaping link is to treat the pole piece with high temperature and high pressure through equipment such as a hot press to fix the shape and size of the pole piece.
.png)
Conclusion
The preparation process of lithium batteries is very complicated, and each step is crucial. Keep an eye on Heltec's blog and we will continue to update you with relevant knowledge about lithium batteries.
Heltec Energy is your trusted partner in battery pack manufacturing. With our relentless focus on research and development, coupled with our comprehensive range of battery accessories, we offer one-stop solutions to meet the evolving needs of the industry. Our commitment to excellence, tailored solutions, and strong customer partnerships make us the go-to choice for battery pack manufacturers and suppliers worldwide.
If you have any questions or would like to learn more, please don't hesitate to reach out to us.
Request for Quotation:
Jacqueline: jacqueline@heltec-bms.com / +86 185 8375 6538
Sucre: sucre@heltec-bms.com / +86 136 8844 2313
Nancy: nancy@heltec-bms.com / +86 184 8223 7713
Post time: Oct-23-2024